LS Central 25.0: Enhancements for fashion and replenishment
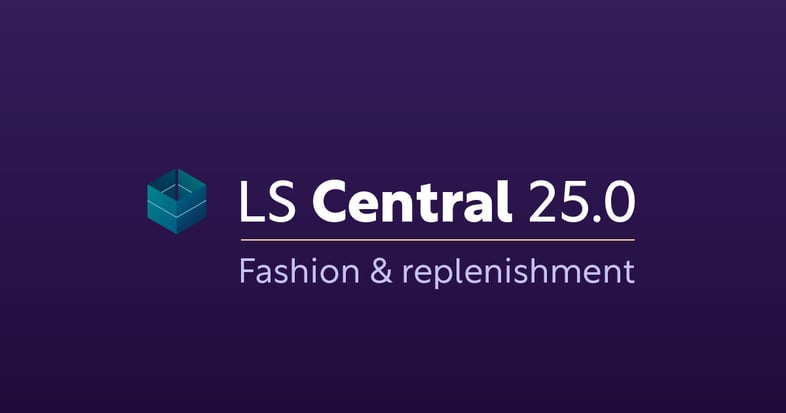
LS Central version 25.0 was released on October 16th, 2024. Here’s an overview of what we have added and improved for fashion and replenishment.
Aggregated Inventory now available for automatic replenishment
Aggregated Inventory was introduced in LS Central version 24.0 as a powerful extension to help retailers with a diverse product-mix more easily track inventory movements at the store level. Now, in LS Central 25.0, Aggregated Inventory for LS Central also supports the automatic replenishment functionality.
Automatic replenishment makes it easier for businesses to calculate the quantity of items needed in stores and the central warehouse to meet customer demand. When using automatic replenishment, retailers can use Aggregated Inventory Entries to calculate inventory, historical sales, quantities on orders, out-of-stock, and more.
Cost redistribution by dimension
Aggregated Inventory tracks details for each store within the Aggregated Inventory Entries. When posting statements, sales from multiple stores are combined into one Item Ledger Entry for the aggregated location. Each store's sales and dimensions are recorded in the Aggregated Inventory Entry, while the total quantity and aggregated location details are stored in the Item Ledger Entry. This links inventory costs in the General Ledger (G/L) to the aggregated location's dimensions.
To distribute these costs to the individual store dimensions, you can use the Cost Redistribution by Dimensions routine. This process finds the relevant G/L accounts, total amounts, and percentage shares for each store, then redistributes the costs from the aggregated dimensions to the specific store dimensions.
Unit cost rollup
Aggregated Inventory for LS Central keeps track of the cost and sales amount in the Aggregated Inventory Entries.
First, the Aggregated Inventory Entries are inserted with the expected cost and sales amount. To update them with the actual costs and sales from the Item Ledger Entries and Value Entries, you can run the Unit Cost Rollup routine. This updates the Aggregated Inventory Entries with the latest data from the linked entries.
Fashion: Simplified mass maintenance of prices for item variants
Maintaining sales prices and purchase prices for item variants is much simpler and faster with the Dimension Price Matrix, which is a tool that provides you with an overview of all the variants belonging to an item. Each item is grouped according to its variant dimensions, for example, by color and size. On the Sales Price List, you can maintain the value for Unit Price, Unit Price Including VAT, and Line Discount %, whereas on the Purchase Price List, you can maintain the value for Direct Unit Cost and Line Discount %.
In the Dimension Price Matrix, you can easily assign a value to the variants or set a new value on existing variants. This will cause the Price List Lines to be created or updated for the variants based on the values that you’ve entered in the matrix. You can also delete the Price List Lines of the variants from the Dimension Price Matrix.
This new functionality is only available if you’ve enabled the new pricing feature for Microsoft Dynamics 365 Business Central.
Replenishment: Improvements to transfer replenishment
We have improved the replenishment journal calculation where it’s now possible to perform transfer replenishment with multiple warehouses and initiate stock transfer between warehouses.
Transfer replenishment with multiple warehouses
You now have the option to replenish your items from up to three warehouses in the Transfer Replenishment Journal calculation. The system will first consume the stock from the primary warehouse and if the demand cannot be fulfilled, it will then take stock from the second warehouse, followed by the third one if needed.
This new feature can be set up and enabled easily. You can either configure a default second and third warehouse for all your items, or you can configure them per destination store, and item group. Afterwards, you just need to enable the replenishment template for which you wish to have the multi-warehouse replenishment feature enabled – and you’re good to go! Furthermore, you can set up the order of the warehouses from which the stock should be taken, either following the default sequence or starting with the warehouse that has the highest or lowest inventory.
Warehouse to warehouse stock transfer
We have introduced a new Warehouse to Warehouse calculation type in the redistribution journal which lets you perform stock transfer between warehouses. Based on the reorder point, maximum inventory, and current stock level of the warehouses, this new calculation type will classify the warehouses into locations with supply or demand in the redistribution journal. With the supply and demand information ready, you can let the system calculate the most efficient way to redistribute items between warehouses, either based on the routes that require minimum trips or costs, as well as those that have the shortest distances or duration.
Replenishment: Improved handling of BOM in BOM effective inventory
A Bill of Materials (BOM) is a product made up of several items, called components. When a component is also made of multiple items, it’s called a BOM in BOM.
We’ve improved our replenishment solution for BOM and components when working with make-to-stock BOM in BOM. When there exists effective inventory for a make-to-stock BOM in BOM, its inventory will be deducted from the calculated demand in the replenishment journal and any assembly orders. As a result, the system will propose the right number of components needed to fulfill the BOM's demand.
We’ve also improved the usability of the replenishment journal to support calculating BOM items assembled in-store, even when some of their BOM in BOM are assembled in the warehouse. In this case, the BOM is handled differently: in the BOM Purchase Replenishment Journal, an assembly order is sent to the warehouse for the BOM in BOM, and in the Component Transfer Replenishment Journal, the BOM in BOM is transferred as a whole item from the warehouse, not broken down into its components.
Replenishment: New automatic release of purchase orders with Release Calendar
Using the new Release Calendar feature, you can automatically release purchase orders at a specific date and time, based on a defined frequency.
Releasing purchase orders automatically and in time
In industries like pharmacies, customers may need items quickly, even if the store is out of stock. Some vendors offer same-day delivery if orders are placed by a certain time. The Release Calendar feature helps by automatically scheduling purchase orders to ensure they're sent to the vendor on time, so the items can reach the store faster.
All you have to do to enable this feature is set up a Release Calendar to define when and how frequent the releases should occur, then link it to a vendor and location. Next, create a scheduler job to process the calendar actions and release purchase orders at the specified date and time.
Releasing purchase orders created from Replenishment Journal
The Release Calendar also works with purchase orders created from the Replenishment Journal. You can let the release process pick up these purchase orders so that they are automatically released as scheduled in the Release Calendar.
Replenishment: Option to choose if logging should be enabled during manual journal calculation
When manually running replenishment calculations with the Add Items to Journal function, you can now choose whether to enable logging for each process using the new Create Calc. Log Lines setting in the report. This setting will be automatically enabled if it's already activated in the Replenishment Setup or Worksheet Batch, but you can change it to overwrite the value. This update applies to all replenishment journal types, including purchase, transfer, BOM, component, and redistribution journals.
Ready to find out how to use your LS Central system to its full potential? Contact our experts to find out more or visit the LS Central Help page.